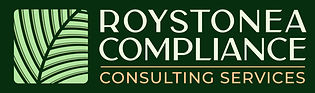
Services
Quality Management System Support
-
Conduct an initial assessment and gap analysis.
-
Develop QMS implementation or upgrade plan.
-
Draft and revise quality documentation, including policies, procedures, and templates.
-
Establish document control processes.
-
Implement core QMS processes like change management, CAPA, and internal audits.
-
Define and monitor key performance indicators (KPIs) to evaluate QMS performance.
-
Facilitate management reviews to discuss QMS performance and improvement opportunities.
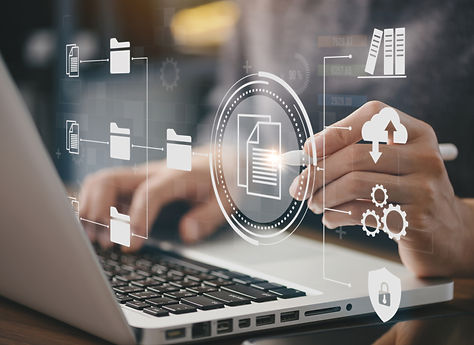
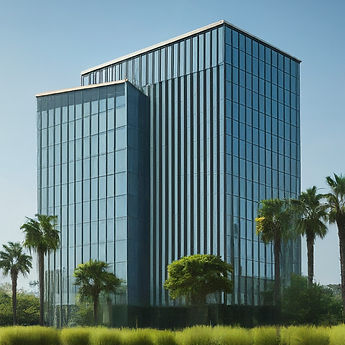
Preparation for Certifications/Inspections
-
Review and update all quality documentation to ensure it meets current regulatory standards.
-
Conduct a mock audit to identify and address potential areas of non-compliance.
-
Ensure all procedures, records, and CAPA documentation are complete, organized, and accessible.
-
Prepare key personnel for interviews by reviewing role-specific questions and responses.
-
Verify that all employee training records are current and relevant to QMS and regulatory requirements.
-
Establish process to handle communication and documentation during the certifications and inspections.
Support for Internal and Supplier Audits
-
Develop an audit schedule and plan based on risk assessment and compliance requirements.
-
Create standardized audit checklists for internal processes and supplier requirements.
-
Conduct audits to evaluate adherence to quality standards and identify process improvements.
-
Document audit findings and prioritize corrective actions for both internal and supplier observations.
-
Track and verify the completion and effectiveness of corrective actions to ensure lasting compliance.
-
Develop tools to maintain records of all audits, findings, and follow-up actions.


Regulations and Standards Compliance Support
-
Identify applicable regulations and industry standards (e.g., ISO, FDA, TGA) for the organization and its products.
-
Conduct a gap analysis to evaluate current compliance status against requirements.
-
Develop or update quality policies and procedures to ensure alignment with regulations.
-
Provide training to staff on regulatory requirements and compliance responsibilities.
-
Assist with audits and inspections by regulatory bodies.
-
Implement corrective actions for any regulatory findings and track progress.
Nonconformance & CAPA Programs Support
-
Establish a standardized process for identifying, documenting, and categorizing nonconformances.
-
Develop templates for NC and CAPA reports to ensure consistency in documentation.
-
Train staff on identifying nonconformances and initiating CAPA investigations.
-
Implement root cause analysis tools (e.g., 5 Whys, Fishbone Diagrams) to determine the cause of nonconformances.
-
Set up tracking and monitoring systems to review NC and CAPA status, timelines, and effectiveness.
-
Establish process to conduct regular reviews to evaluate CAPA effectiveness and identify recurring issues

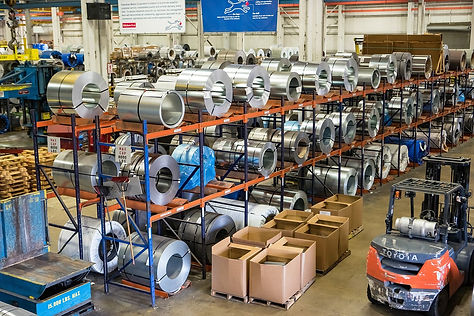
Supplier Quality Program Support
-
Define supplier quality requirements and criteria based on standards and regulatory requirements.
-
Develop a supplier qualification and onboarding process, including assessments and audits.
-
Create a supplier performance monitoring system with key performance indicators (KPIs).
-
Establish a process for managing and addressing supplier nonconformances and corrective actions.
-
Implement supplier scorecard to track performance and support continuous improvement.
-
Conduct regular supplier audits and reviews to ensure adherence to quality standards.
-
Provide training and resources to suppliers on quality expectations and regulatory requirements.
Document and Change Control Programs Development
-
Establish document control procedures, including version control, approval workflows, and access permissions.
-
Develop templates and naming conventions to standardize documentation across the organization.
-
Implement a centralized system for storing, managing, and retrieving controlled documents.
-
Define change control procedures, including change request initiation, impact assessment, and approval steps.
-
Set up tracking for document revisions and changes to maintain audit trail.
-
Train employees on document control and change management processes.
-
Establish process to conduct periodic reviews to ensure document accuracy and relevance, removing obsolete documents when needed.
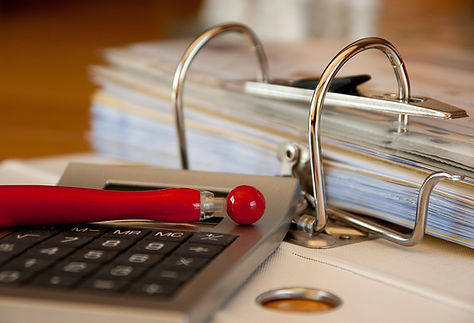
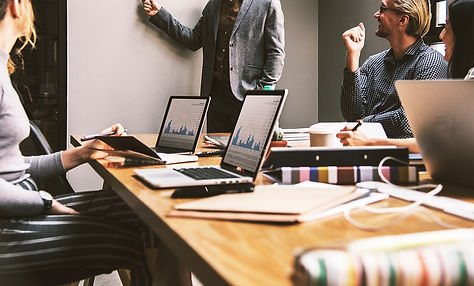
Risk Management and Mitigation
-
Identify and document potential risks across processes, products, suppliers, and regulatory compliance.
-
Perform risk assessments using tools like Failure Modes and Effects Analysis (FMEA) or risk matrices to evaluate impact and likelihood.
-
Develop risk mitigation strategies, including preventive actions and controls to minimize risk occurrence.
-
Implement monitoring systems to track key risk indicators and detect early warning signs.
-
Establish a process for reviewing and updating risk assessments periodically and after significant changes.
-
Conduct risk management training for staff to ensure awareness and adherence to mitigation processes.
Feedback & Complaint Management Program Deployment
-
Assess current feedback and complaint management processes, identifying gaps and improvement areas.
-
Develop and implement a standardized process for logging, categorizing, and tracking customer complaints.
-
Guide the organization in establishing clear timelines, roles, and responsibilities for efficient complaint. acknowledgment, investigation, and resolution.
-
Conduct training sessions on root cause analysis techniques to address underlying issues and prevent complaint recurrence.
-
Set up complaint tracking and monitoring tools to analyze metrics, identify trends, and drive continuous quality improvements.
-
Ensure documentation practices comply with regulatory requirements.


Asset Management Program Support
-
Develop an asset inventory system and define procedures to track equipment details, location, and maintenance requirements.
-
Establish calibration and preventive maintenance (PM) schedules based on equipment specifications and usage.
-
Implement a tracking system for calibration and PM activities to ensure timely and accurate servicing.
-
Define procedures for managing and investigating impact of out-of-tolerance conditions.
-
Train staff on proper asset handling, maintenance, and calibration processes.
Equipment Qualification, Computerized System and Software Validation
-
Develop and implement equipment qualification processes.
-
Establish a validation process for computerized systems and software that meets regulatory requirements (e.g., GxP, FDA 21 CFR Part 11).
-
Implement a risk-based approach to prioritize qualification and validation activities.
-
Create standardized testing and documentation processes to validate system functionality, security, data integrity, and compliance.
-
Develop change control processes to manage updates or modifications to qualified equipment and validated systems, maintaining compliance and documentation accuracy.
